top of page


Production of Sustainable Surgical Face Mask Using Poplar Fibers
Popmask is a surgical mask made of sustainable and natural poplar fibers. Poplar fibers have hollow lumen and highly hydrophobic. In this study, poplar fibers were turned into wet-laid webs for the first time. These webs were employed as filtration media in surgical mask. Production method of POPMASK is described in the below preprint.
Rapid -Köthen automatic sheet forming machine was used to create wet-laid webs made of 100% poplar fibers. Fiber weight vs web weight/density table is seen below:
Table 1. Weight of the employed fiber amount in the PTA Rapid - Köthen automatic sheet forming machine and the weight of the resultant samples.
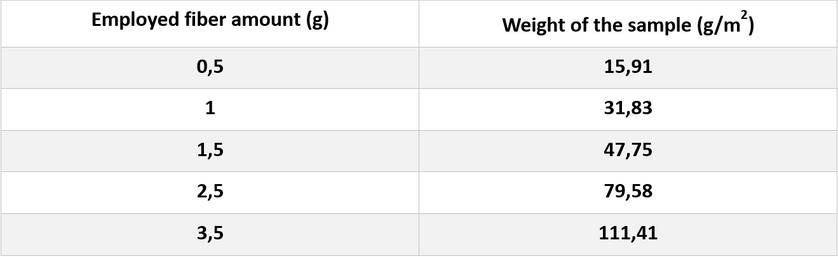
Commercial surgical masks are formed out of 3 layers. The inner filtration media usually have a weight of 15-27 g/m2. For this reason, 0.7 g of fibers were employed in the production of the wet laid web. Wet laid formation is shown in Figure 1.

Figure 1. Developing 100% poplar wet laid webs using the Rapid -Köthen automatic sheet forming machine.
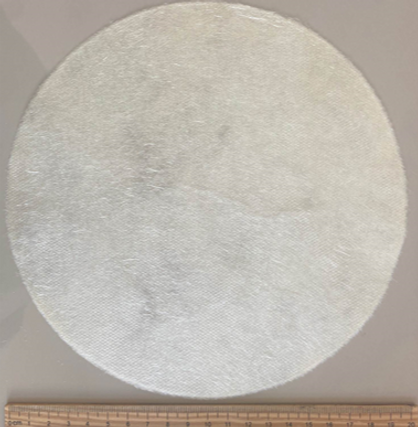
Figure 2. Resulted poplar web.
To produced the webs shown in Figure 2, surfactants were employed to prevent adhesion of the fibers on the machine’s glass walls. After obtaining these webs, they were also rinsed and pressed. To see the effect of the rinsing and pressing steps, filtration performance of 3 different webs were measured as shown in Table 2.
Bacterial filtration efficiencies of rinsed, unrinsed, and pressed samples were measured according to the EN14683 standards. Bacterial filtration efficiency of the pressed samples was the highest. All 3 samples have sufficient efficiency to capture 3-micron particles in the test.

Results given in Table 2 clearly indicated that these webs can be good candidate for employing as a surgical face mask. To develop a Popmask prototype, following steps were conducted.
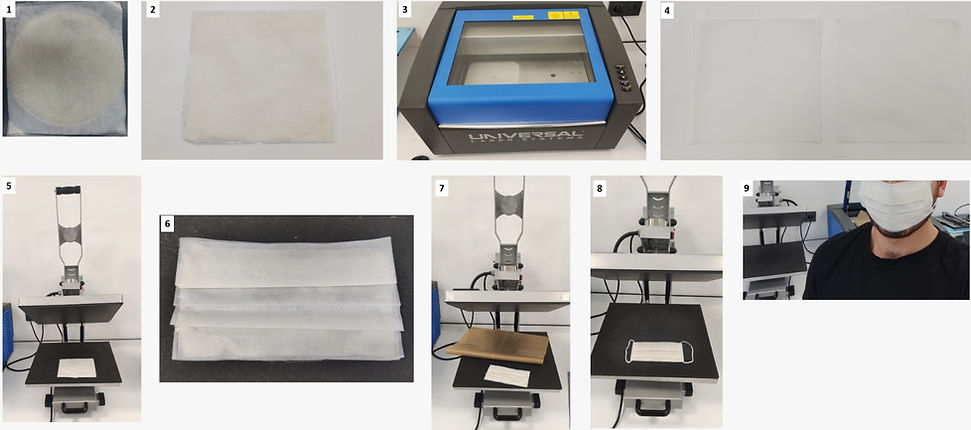
Figure 3. POPMASK surgical mask prototype production steps.
Following the manufacturing of the wet laid samples shown in Figure 2, one poplar nonwoven fabric was placed between the commercial spun-bond PP nonwovens and a final prototype was made as explained in Figure 3. In order to cut precise dimensions, a laser cutting machine was used, and for the drawings, Corel Draw software was utilized. PP webs were cut into 16x16 cm pieces, while the wet laid web was cut into 15.5x15.5 cm. After cutting the fabrics into the desired dimensions, all the layers and fusible sheets were placed under the heat press machine. To avoid damaging the poplar fibers with high temperatures, we used low-melting-point, double-sided fusible layers, which have a lower melting point compared to polypropylene itself. Webs were folded and hot-pressed as shown in Figure 3, image #6, and then hot pressed for fixation. During this process, elastic cords were also attached to both sides of the produced face mask that has dimensions of 4x8.5 cm. Final Popmask surgical mask prototype is seen in Figure 4.

Figure 4. Final prototype of POPMASK surgical mask.
“This project has received funding from the European Union’s Horizon 2020 research and innovation programme under the Marie Sklodowska-Curie grant agreement No 101023459”
bottom of page